مراحل تولید سیمان در کارخانه های ایران
مراحل تولید سیمان در کارخانه های ایران؛ گام به گام از سنگ تا سازه
سیمان یکی از حیاتی ترین مصالح در صنعت ساخت و ساز مدرن است و نقش بنیادینی در شکل گیری زیرساخت ها و سازه های امروزی ایفا می کند. این ماده پودری که با آب ترکیب شده و پس از گیرش به ماده ای سخت و مقاوم تبدیل می شود حاصل یک فرآیند پیچیده و دقیق صنعتی است. شناخت این فرآیند نه تنها برای متخصصان حوزه عمران و معماری بلکه برای تمامی علاقه مندان به درک چگونگی ساخت جهان پیرامون ما جذاب و آموزنده است.
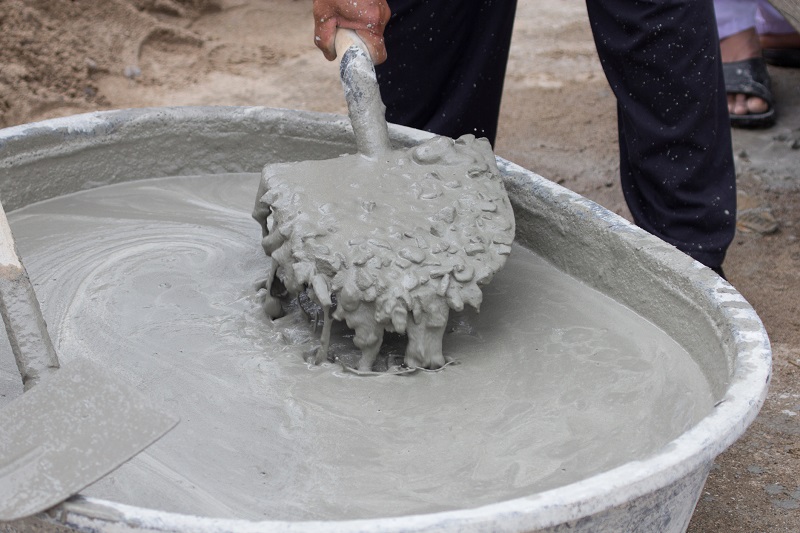
در ایران با توجه به وجود منابع غنی مواد اولیه و سابقه طولانی در صنعت سیمان کارخانه های متعددی با بهره گیری از تکنولوژی های روز دنیا به تولید انواع سیمان مشغول هستند. فرآیند تولید سیمان در این کارخانه ها شامل مجموعه ای از مراحل پیوسته و کنترل شده است که از استخراج مواد اولیه از معادن آغاز شده و تا بسته بندی محصول نهایی ادامه می یابد. در این مقاله به صورت جامع و تخصصی به بررسی این مراحل در کارخانه های سیمان ایران خواهیم پرداخت و جزئیات هر گام را تشریح می کنیم. قیمت سیمان اصفهان از الومتریال از طریق ارتباط باکارشناسان به صورت هفتگی قابل استعلام است و در صورت موجود بودن با بهترین قیمت قابل خریداری است.
مواد اولیه تولید سیمان
تولید سیمان پرتلند که رایج ترین نوع سیمان در ایران و جهان است عمدتاً به چهار عنصر اصلی وابسته است: کلسیم سیلیس آلومینیوم و آهن. این عناصر از مواد طبیعی مختلفی که در معادن یافت می شوند تامین می گردند. ترکیب دقیق این مواد اولیه نقش حیاتی در کیفیت و خواص نهایی سیمان دارد.
مواد اولیه کلیدی مورد استفاده در کارخانه های سیمان ایران شامل موارد زیر است:
- سنگ آهک (Calcium Carbonate – CaCO3): اصلی ترین منبع کلسیم که بیشترین سهم را در ترکیب مواد خام دارد. معادن سنگ آهک با خلوص بالا در نقاط مختلف ایران وجود دارند.
- رس (Clay): منبع اصلی سیلیس آلومینیوم و مقداری آهن. رس ها معمولاً در مجاورت معادن سنگ آهک یافت می شوند.
- سنگ آهن (Iron Ore): برای تنظیم میزان آهن و کمک به فرآیند پخت کلینکر استفاده می شود.
- بوکسیت یا سنگ معدن آلومینیوم (Bauxite): برای تنظیم میزان آلومینیوم در ترکیب مواد خام به ویژه در تولید سیمان های خاص.
- سیلیس (Silica – SiO2): ممکن است به صورت سنگ سیلیس یا ماسه سیلیسی به ترکیب اضافه شود تا نسبت سیلیس به سایر اجزا تنظیم گردد.
ترکیب این مواد باید با دقت محاسبه و کنترل شود تا نسبت های شیمیایی مورد نیاز برای تولید کلینکر سیمان پرتلند حاصل گردد. این ترکیب به اصطلاح «خوراک کوره» نامیده می شود و کیفیت آن مستقیماً بر راندمان کوره و کیفیت نهایی سیمان تاثیر می گذارد.
مرحله استخراج و آماده سازی مواد اولیه
اولین گام در فرآیند تولید سیمان استخراج مواد اولیه از معادن اطراف کارخانه است. این مواد شامل سنگ آهک رس و سایر افزودنی های معدنی مورد نیاز هستند. استخراج معمولاً با استفاده از ماشین آلات سنگین مانند بیل مکانیکی و کامیون های عظیم صورت می گیرد.
پس از استخراج مواد اولیه به محل ذخیره سازی در کارخانه منتقل می شوند. در این مرحله ممکن است نیاز به آماده سازی اولیه مانند همگن سازی یا تفکیک مواد بر اساس کیفیت باشد. هدف اصلی در این مرحله تامین مداوم و یکنواخت مواد اولیه برای مراحل بعدی تولید است.
مرحله خردایش (Crushing)
مواد اولیه استخراج شده به ویژه سنگ آهک معمولاً در ابعاد بسیار بزرگ هستند و برای ورود به مراحل بعدی فرآیند باید خرد شوند. این عملیات در بخش سنگ شکن کارخانه انجام می شود.
سنگ شکن های اولیه (مانند سنگ شکن فکی یا چکشی) ابعاد بزرگ سنگ ها را به قطعات کوچک تر (معمولاً در حد چند سانتی متر) کاهش می دهند. در برخی کارخانه ها از سنگ شکن های ثانویه نیز برای کاهش بیشتر ابعاد استفاده می شود. هدف از خردایش آماده سازی مواد برای ورود به آسیاب های مواد خام است.
مرحله آسیاب مواد خام (Raw Material Grinding)
پس از خردایش مواد اولیه خرد شده به نسبت های مشخصی که توسط آزمایشگاه کنترل کیفیت تعیین شده است مخلوط شده و وارد آسیاب های مواد خام می شوند. در کارخانه های مدرن ایران عمدتاً از فرآیند خشک برای تولید سیمان استفاده می شود بنابراین مواد خام به صورت پودر خشک آسیاب می شوند.
آسیاب های مواد خام معمولاً از نوع گلوله ای (Ball Mill) یا عمودی (Vertical Roller Mill – VRM) هستند. این آسیاب ها مواد را به پودری بسیار نرم و یکنواخت تبدیل می کنند که به آن «خوراک خام» یا «پودر خام» گفته می شود. نرمی این پودر نقش مهمی در فرآیند پخت در کوره دارد.
پس از آسیاب پودر خام به سیلوهای همگن سازی منتقل می شود. در این سیلوها با استفاده از هوای فشرده پودر خام به صورت مکانیکی و پنوماتیکی مخلوط می شود تا ترکیب شیمیایی آن در تمام حجم سیلو یکنواخت گردد. این همگن سازی برای اطمینان از پایداری فرآیند پخت و کیفیت نهایی کلینکر حیاتی است.
مرحله پخت و تولید کلینکر (Burning and Clinker Production)
قلب فرآیند تولید سیمان مرحله پخت در کوره دوار است. پودر خام همگن شده وارد کوره دوار می شود. کوره دوار یک استوانه فلزی بزرگ و شیب دار است که به آرامی حول محور خود می چرخد و دمای آن به تدریج از ابتدای کوره به سمت انتهای آن افزایش می یابد. از طریق یوتیوپ می توانید با ویدئوهای مربوط به سیمان آشنا شوید.
در طول مسیر حرکت پودر خام در کوره واکنش های شیمیایی مختلفی رخ می دهد:
- خشک شدن: ابتدا رطوبت باقی مانده در پودر خام تبخیر می شود.
- کلسیناسیون: در دمای حدود 800-900 درجه سانتی گراد کربنات کلسیم (CaCO3) موجود در سنگ آهک تجزیه شده و به اکسید کلسیم (CaO) و دی اکسید کربن (CO2) تبدیل می شود. این واکنش مهم ترین مرحله در کوره است.
- کلینکریزاسیون: در منطقه پخت با دمای حدود 1400-1450 درجه سانتی گراد اکسید کلسیم با سیلیس آلومینیوم و آهن واکنش داده و فازهای اصلی تشکیل دهنده کلینکر سیمان (مانند آلیت بلیت آلومینات و فریت) تشکیل می شوند. این فازها به صورت گرانول های سخت و متخلخل به نام کلینکر ظاهر می شوند.
سوخت مورد استفاده در کوره های سیمان ایران متنوع است و شامل گاز طبیعی مازوت کک نفتی و حتی سوخت های جایگزین مانند زباله های صنعتی و شهری فرآوری شده می شود. انتخاب سوخت بر اساس دسترسی و ملاحظات اقتصادی و زیست محیطی صورت می گیرد.
مرحله خنک کردن کلینکر (Clinker Cooling)
کلینکر داغ خروجی از کوره (با دمای حدود 1000-1200 درجه سانتی گراد) باید به سرعت خنک شود. این کار در خنک کن های کلینکر (معمولاً از نوع گریت یا سیاره ای) انجام می شود. خنک کردن سریع باعث تثبیت فازهای تشکیل شده در کلینکر و افزایش قابلیت آسیاب شدن آن می شود.
هوای گرم خروجی از خنک کن کلینکر که انرژی زیادی دارد معمولاً مجدداً به عنوان هوای ثانویه یا ثالثیه وارد کوره می شود تا به افزایش راندمان حرارتی و کاهش مصرف سوخت کمک کند. این بازیابی حرارت یکی از ویژگی های مهم فرآیند خشک در کارخانه های سیمان مدرن ایران است.
مرحله آسیاب کلینکر و افزودنی ها (Clinker and Additives Grinding)
کلینکر خنک شده به همراه مقادیر مشخصی از مواد افزودنی وارد مرحله آسیاب نهایی می شود. اصلی ترین افزودنی در این مرحله سنگ گچ (Calcium Sulfate – CaSO4) است که برای تنظیم زمان گیرش سیمان اضافه می شود.
سایر افزودنی ها ممکن است شامل پوزولان ها (مانند خاکستر بادی سرباره کوره بلند سیلیس فوم یا پوزولان های طبیعی) سنگ آهک یا سایر مواد معدنی باشند که برای تولید انواع خاصی از سیمان یا بهبود خواص آن اضافه می شوند. نسبت کلینکر به افزودنی ها نوع سیمان نهایی را تعیین می کند (مانند سیمان پرتلند تیپ 2 تیپ 5 پوزولانی و … مطابق با استاندارد ملی ایران).
آسیاب نهایی نیز معمولاً توسط آسیاب های گلوله ای یا آسیاب های عمودی انجام می شود. هدف در این مرحله تولید پودری بسیار نرم و یکنواخت به نام سیمان است. نرمی سیمان بر سرعت هیدراتاسیون و مقاومت اولیه آن تاثیر می گذارد.
مرحله انبارش و بسته بندی (Storage and Packaging)
سیمان تولید شده پس از آسیاب نهایی به سیلوهای بزرگ سیمان منتقل می شود. این سیلوها برای ذخیره سازی ایمن سیمان در برابر رطوبت و آلودگی طراحی شده اند.
از سیلوها سیمان می تواند به صورت فله ای (برای پروژه های بزرگ یا حمل با تانکر) یا به صورت بسته بندی شده (در کیسه های 25 یا 50 کیلوگرمی) برای توزیع به بازار مصرف ارسال شود. فرآیند بسته بندی توسط دستگاه های اتوماتیک انجام می شود.
کنترل کیفیت در تولید سیمان
کنترل کیفیت یک فرآیند مستمر در تمامی مراحل تولید سیمان است از استخراج مواد اولیه تا محصول نهایی. آزمایشگاه های کنترل کیفیت در کارخانه های سیمان ایران نقش حیاتی ایفا می کنند.
آزمایش های شیمیایی و فیزیکی به طور منظم بر روی مواد اولیه خوراک خام کلینکر و سیمان نهایی انجام می شود. این آزمایش ها شامل تعیین ترکیب شیمیایی نرمی استحکام فشاری زمان گیرش و سایر خواص مطابق با استانداردهای ملی ایران (مانند استاندارد ملی 389) و استانداردهای بین المللی است. هدف از کنترل کیفیت اطمینان از تولید سیمانی با کیفیت ثابت و مطابق با مشخصات فنی مورد نیاز است. همانطور که می دانید قیمت سیمان باکیفیت به مراتب بالاتر از سیمان بی کیفیت است. اما یک انتخاب مطمئن و دائمی برای پروژه های شما است.
سوالات متداول درباره تولید سیمان در ایران
فرآیند خشک در تولید سیمان چیست؟
فرآیند خشک روشی نوین و کم مصرف تر در تولید سیمان است که در آن مواد اولیه به صورت پودر خشک آسیاب و پخت می شوند برخلاف فرآیند تر که مواد اولیه به صورت دوغاب وارد کوره می شوند.
کلینکر سیمان چیست؟
کلینکر گرانول های سخت و متخلخلی هستند که پس از پخت پودر خام در کوره سیمان در دمای بالا تشکیل می شوند و ماده اصلی تشکیل دهنده سیمان پرتلند محسوب می شوند.
نقش سنگ گچ در تولید سیمان چیست؟
سنگ گچ به عنوان یک افزودنی در مرحله آسیاب نهایی به کلینکر اضافه می شود تا زمان گیرش سیمان را تنظیم کرده و از گیرش ناگهانی آن جلوگیری کند.
اهمیت همگن سازی پودر خام چیست؟
همگن سازی پودر خام برای اطمینان از یکنواختی ترکیب شیمیایی آن قبل از ورود به کوره ضروری است که این امر پایداری فرآیند پخت و کیفیت نهایی کلینکر را تضمین می کند.
چه نوع سوخت هایی در کوره های سیمان ایران استفاده می شود؟
در کارخانه های سیمان ایران از انواع سوخت ها شامل گاز طبیعی مازوت کک نفتی و همچنین سوخت های جایگزین فرآوری شده استفاده می شود.
آیا شما به دنبال کسب اطلاعات بیشتر در مورد "مراحل تولید سیمان در کارخانه های ایران" هستید؟ با کلیک بر روی اقتصادی, کسب و کار ایرانی، آیا به دنبال موضوعات مشابهی هستید؟ برای کشف محتواهای بیشتر، از منوی جستجو استفاده کنید. همچنین، ممکن است در این دسته بندی، سریال ها، فیلم ها، کتاب ها و مقالات مفیدی نیز برای شما قرار داشته باشند. بنابراین، همین حالا برای کشف دنیای جذاب و گسترده ی محتواهای مرتبط با "مراحل تولید سیمان در کارخانه های ایران"، کلیک کنید.